Tungsten Cemented Carbide Grade
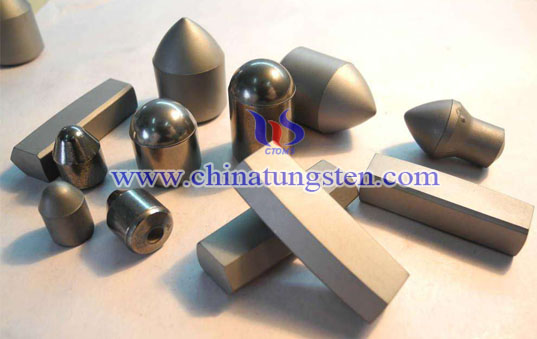
How to choose the proper tungsten cemented carbide?
Selecting the proper tungsten carbide grade boils down to an educated compromise. The specifier, aware that no metal offers the ultimate in everything desired, must determine what properties are needed most, and then strike the balance that best meets his or her needs. How much toughness is needed? What about resistance to corrosion and shock? How important is wear and abrasion resistance? What design parameters must be considered? What are the applied loads and stresses? Is edge preparation a consideration?
Then add to this matrix considerations such as tungsten cemented carbide grain size, binder alloy percentage, and the addition of titanium, tantalum carbide, and other alloying elements. All of these variables have to be calculated to achieve the best compromise and result.
In general, many variables and conditions have to be considered in selecting the proper tungsten cemented carbide grade for tool, die and wear part applications. Every application should be evaluated carefully and individually to optimize the composition most likely to provide the right balance of hardness, wear, strength, toughness and corrosion resistance.
Tungsten cemented carbide grade, performance and applications
Grade |
Typical property values |
Performance & Applications |
||
Density |
Bending |
Hardness |
||
Z10 |
14.85~15.0 |
1800~2100 |
88.5~91.0 |
High wear resistance, for pillar bit drills. |
Z20 |
14.65~14.85 |
2100~2500 |
87.5~89.0 |
Excellent wear resistance and toughness, for pillar bit drills. |
Z25 |
14.45~14.65 |
2300~2700 |
86.5~88.0 |
Of high toughness and wear resistance as well as good versatility, for rotary hammer rock drill bits and pillar bit drills, for f14~f16 medium hard and hard rock formations. |
Z30 |
14.4~14.6 |
2350~2800 |
86.0~87.5 |
High toughness and wear resistance and good versatility, for rotary hammer rock drill bits and heavy rock drill bits, for f16~f18 hard and medium hard rocks formations. |
K05 |
14.4~14.7 |
2200 |
>=87.5 |
High toughness, wear resistance and performance, for single line and cross bits of rotary hammer rock drills for hard rock formations. |
K510 |
14.5~14.8 |
2100~2600 |
>=88.5 |
High toughness and wear resistance, for pillar picks and coal cutting picks. |